Distillation technology is the most important technology to achieve mixture separation by using the different boiling points of each component in the mixture. The boiling points of each component are different. When they are in a state of gas-liquid coexistence, the components with low boiling point are relatively volatile, so the relative proportion of the components with low boiling point in the gas phase is higher than that of the components with low boiling point in the liquid phase. This property of binary mixture can be used to achieve complete separation of binary mixture by distillation. Binary mixture distillation separation process includes the following standard equipment, one is the distillation of raw materials (binary mixture) transport, if the boiling point of the binary mixture at room temperature (ambient temperature) below, the binary mixture at room temperature gaseous transport equipment is a compressor, if the binary mixture boiling point above room temperature, the binary mixture at room temperature liquid transport equipment is a pump. The second is the heat exchange of the binary mixture of distillation raw materials and distillation separation products, and this heat exchanger can also be called the main heat exchanger. Its main function is through the heat exchange of distillation raw materials and distillation separation products, on the one hand, the distillation raw materials after heat exchange into the middle of the rectification column in a state close to gas-liquid coexistence, on the other hand, the temperature of distillation separation products after heat exchange close to normal temperature for storage and transportation, of course, the heat exchange of distillation raw materials and distillation separation products also reduces the energy consumption of distillation separation process. The third is the distillation column, which is the core part of the distillation separation process, and the distillation separation of the binary mixture is realized in the distillation column. It consists of three parts, one is set on the top of the distillation column condenser, through cooling water to provide cooling capacity to condense the low boiling point components in the distillation column into liquid phase as the reflux liquid of the distillation column. The second is the reboiler set at the bottom of the rectification column, which provides heat through steam to evaporate and rise the high-boiling components at the bottom of the rectification column as distillation gas. The third is the distillation column body, which is a cylindrical pressure vessel with a tray or packing in the middle. The role of the tray and packing is to strengthen mass and heat transfer so that distillation separation can be carried out, so that low boiling point pure components and high boiling point pure components can be extracted from the top and bottom of the rectification column. Distillation is a basic chemical unit operation, it is a purely physical process, there is no mystery! As can be seen from the above description, the heat input by the reboiler steam is basically taken away by the cooling water of the condenser! Therefore, the distillation separation process does not actually consume heat, it consumes the effective energy generated by the temperature difference between the input heat of the reboiler and the output heat of the condenser, which lays the most important foundation for the heat pump technology to be widely used in the distillation separation process and become the most important energy-saving technology in the distillation separation process. The most basic application of heat pump technology in the distillation separation process is to use closed heat pump instead of steam and cooling water to heat the reboiler and output heat from the condenser. This most basic application does not change the equipment of the distillation column and the parameters in the distillation column, and it is still a standard single-column distillation separation process for the distillation separation process of binary mixtures. Although the use of closed heat pump instead of steam and cooling water is the most basic way of heat pump technology used in the distillation separation process, it is not common in the actual distillation separation process! The reasons are as follows: First, the closed heat pump is only suitable for the binary mixture of high boiling point components boiling point and low boiling point components boiling point gap is not too large, the boiling point gap is too large, the compression ratio of the heat pump compressor is too large, the project cost will rise significantly, the economy is not favorable! The second is to completely replace steam and cooling water with closed heat pump to heat the reboiler and output heat from the condenser, which will inevitably bring about the problem of heat balance or cold balance of the rectification system, and in order to ensure the heat balance of the rectification system, in the case that steam and cooling water can be used to achieve distillation separation, the simplest way is to still retain the reboiler and condenser using steam and cooling water. In this case, the use of closed heat pump completely self-heating distillation separation process is not necessary, only need to use single heat pump and multi-heat pump technology to improve the distillation separation process! Third, the use of open heat pumps in the distillation separation process has great advantages over closed heat pumps. Fourth, the use of closed heat pump distillation process is only more suitable near the ambient temperature, and it is difficult to find a suitable cycle working medium if it is too far away from the ambient temperature. For the above reasons, closed heat pumps are widely used only when the boiling point of a binary mixture is near room temperature. The most widely used in the distillation separation process is the so-called single heat pump and multi-heat pump technology, the so-called single heat pump and multi-heat pump technology is an open heat pump! It leads the mixture from the rectification section of the distillation column to the heat pump compressor after compression, in the distillation section of the distillation column set in the heat exchanger with the mixture of liquid falling in the distillation column, on the one hand, the liquid in the distillation column and its own liquefaction after decompression into the distillation section of the distillation column as reflux liquid. Single heat pump and multi-heat pump technology is not only suitable for the energy saving transformation of conventional distillation separation process, but also suitable for the energy saving transformation of heat pump distillation process! So its use is the most widespread and the most common. The third way that heat pump technology is used in the distillation separation process is the so-called open heat pump distillation process, the so-called self-heating distillation process, in the single heat pump and multi-heat pump distillation technology, the circulating working medium of the single heat pump and multi-heat pump is the intermediate product of the distillation process, if we use the distillation raw materials and low-boiling point components as the circulating working medium of the heat pump, Then it is possible to find three open heat pump distillation processes that can be realized, of which two open heat pump distillation processes with rectification raw materials as the circulating working medium are respectively the open heat pump distillation single-tower process of producing a single pure component, and the open heat pump distillation two-tower process that can realize the complete separation of two components. Another open heat pump rectifying single-column process with low boiling point pure composition of circulating working medium. Of course, the open heat pump distillation process is not unlimited. Under normal circumstances, it is only suitable for the boiling point of the binary mixture below room temperature, only in this case, the distillation mixture and low boiling point distillation pure components are gaseous at room temperature, suitable for compression at room temperature. Secondly, in this case, in addition to the use of heat pumps, there is no feasible way to achieve the industrial operation of distillation separation, which is to some extent, the Liangshan! A very important problem in open heat pump distillation process is how to achieve the balance of cooling capacity. This is actually the case with cryogenic air separation!
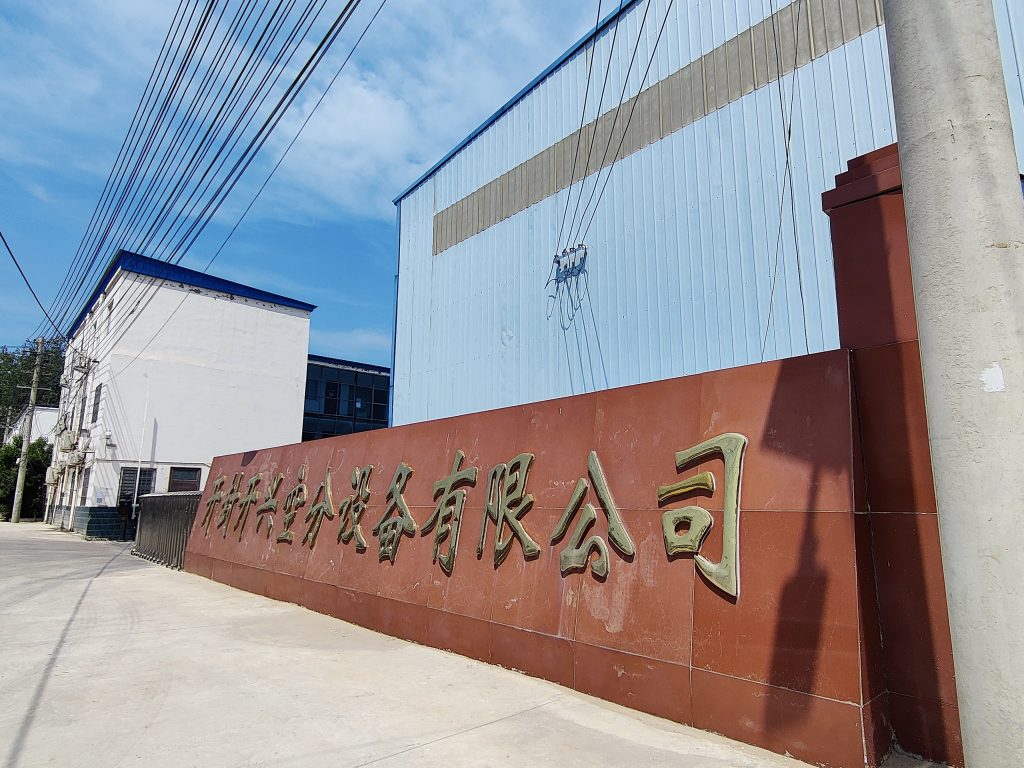